PVTIME – Against the background of the global trend towards grid parity, the upgrading of solar wafer size from 156.78mm to larger sizes — including 158.75mm, 166mm, or even 210mm — has become a controversial topic in the PV industry. Top module and cell suppliers, including Jinko, JA Solar, Trina Solar and Aiko Solar, have retrofitted their in-house cell production lines to be compatible with the full square mono 158.75mm wafers, while LONGi and Zhonghuan Semiconductor have been promoting the 166mm and 210mm wafers respectively. As the solar industry moves towards adopting larger wafers, no consensus has yet been reached between producers on wafer size.
PVInfoLink predicts that “158.75 modules” (modules with full square mono 158.75mm cells) will dominate the market in the first half of 2020, and the market is expected to see an increase of “166 modules” (modules with 166mm cells) in the second half of 2020 when LONGi, Canadian Solar, and Risen Energy put their 166mm products into mass production. However, it is still unclear whether or not more producers will follow suit. Industry experts estimate that, by 2020, the market share of “158.75 modules” could reach 60%, and the M2 (156.75mm) series will become obsolete .
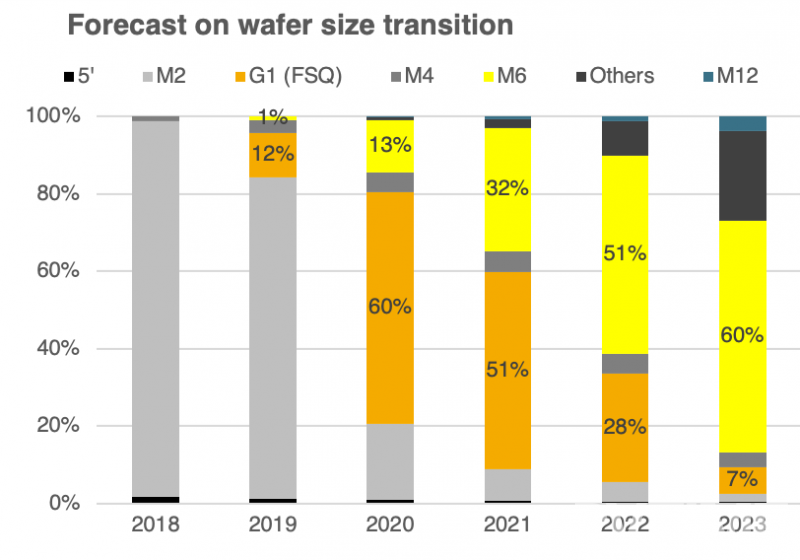
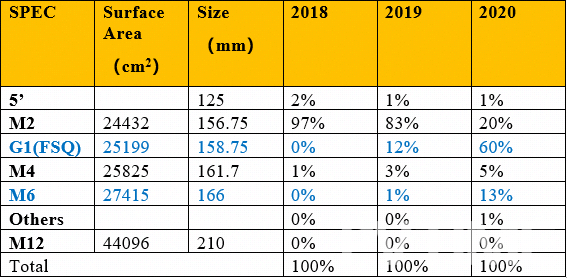
Why full square mono 158.75mm cells will dominate the market in 2020
According to Zhiyu Zhang, an analyst from Solarwit, “modules with full square mono 158.75mm cells are bound to dominate the market with the constant cost decline of crystal growth techniques, making the benefits outweigh costs while shifting pseudo-square wafers to full square wafers. Full square wafers fit onto PV modules in an optimal way and raises the conversion efficiency significantly.” Zhang added that, “the 158.75mm square wafer is 3.14% larger than M2, and increases the power of the same-size cell by around 0.15W. In other words, with little change to the size of modules, the 158.75mm wafers raise the power output of conventional 60-cell modules from 310W to 320W, and enables 72-cell modules to reach 410W.”
In summary, module with full square mono 158.75mm cells have a larger light receiving area and higher power output with very little incremental cost.
Industry experts concur that the increase of wafer size is an inevitable trend, but an excessive increase would exert great pressure on manufacturers. Retrofitting current production lines to be compatible with 166mm and 210mm is considerably more costly than retrofitting to 158.75mm. For 158.75mm cell production, automation equipment and fixtures need to be adjusted, and the cost of which is rather low when shared equally into the cost per watt; for module production, all changes are made in the production line’s carrier and welding segments, and the sizes of auxiliary materials including EVA, back sheet and glass will increase.
In contrast, retrofitting the production line to be compatible with 166mm is much more costly. Cell production requires updating current automation equipment, and purchasing of new tubular PECVD and auxiliary equipment. For the production of 166 modules, series welding, stitch welding, laminating, and framing machinery will need to be replaced, and the assembly line has to be upgraded and retrofitted. Data from PVInfoLink shows that the retrofitting cost to 166mm cells and modules is 2-3 times higher than that of retrofitting to 158.75mm. This explains why LONGi and its downstream cell factories are currently the only producers of 166mm products .
Additionally, during the mass production of 166mm and 210mm wafers and cells, solar manufacturers will face more challenges including, (i) higher breakage rate during the wafer slicing process; (ii) higher risk of wafer distortion; (iii) wafer cohesion in neighboring quartz boats in the diffusion process; and (iv) lower cell efficiency caused by uneven surfaces during the texturing and coating processes. Although the yield of 166mm production lines can be improved through retrofitting, it would result in a 20% loss if it’s upgraded from a 156.75mm production line.
Currently, through analyzing the pros and cons of each size, the market seems to be moving forward with 158.75mm as the mainstream choice. Given its advantages of low retrofitting costs, lower cost per watt, and higher power output through shifting pseudo-square wafers to full square wafers, the 158.75mm products represent the best choice for investors pursuing solar modules with higher efficiency, power output, and cost to performance.