PVTIME – China’s National Development and Reform Commission (NDRC) has issued a consultation document to solicit advice for the 2020 policy on the prices of electricity generated by photovoltaic plants. According to the consultation paper, the tariffs of newly-built ground-mounted power stations in three resource areas of the country are set at 0.35 yuan/kWh, 0.4 yuan/kWh, and 0.49 yuan/kWh, respectively (unless indicated otherwise, tax is included in the tariffs). Meanwhile, the tariff of industrial and commercial distribution plants is set at 0.05 yuan/kWh, and the subsidy for household solar plant is 0.08 yuan/kWh. Although the tariff is higher than previously expected, grid parity for photovoltaics and price bidding remain key topics this year.
National Energy Administration (NEA) will continue to implement the overall plan outlined in 2019 to support and prioritize the construction of unsubsidized (grid-parity) projects. To reach grid parity, it’s important for photovoltaic enterprises to choose modules with “low cost, high power, and high power generation” as modules account for 47% of the system cost of a solar plant.
Starting from early 2019, Jinko, JA Solar, Trina Solar, and Risen Energy have retrofitted their production lines of 156.75mm wafers, cells and related modules to those of 158.75mm products. The new production line significantly improves module power with relatively low transformation cost and little retrofitting difficulty. Most tier-one enterprises have completed the conversion to 158.75mm products, and have started supplying the products to the market.
According to PVInfoLink, the market share of 158.75mm silicon wafers is expected to reach 60% in 2020. As for larger 166mm and 210mm products, most enterprises are still in the wait-and-see stage.
To maximize the advantages of 158.75mm products in energy yielding, producers choose to combine 158.75mm x 158.75mm cells with MBB and half-cell technology. The combination has proved successful and is gaining market share. According to PVInfoLink, suppliers including Jinko, JA Solar, Risen Energy, and Trina Solar are promoting modules assembled with half-cut MBB 158.75mm cells.
Tested by some Chinese producers as early as in 2016 to further improve cell efficiency, MBB technology has been developed and applied on a large scale by leading module manufacturers since 2019. The technology increases module power significantly with its round busbar and closer busbar design.
Compared with conventional busbar design, the round busbar design used in MBB cells reduces shading area and effectively reflects sunlight to the cell to increase short-circuit current of the module. The “double” light reflection of the round busbar boosts light absorption and utilization rate of the cell by increasing the optical utilization rate of the busbar area from less than 5% to over 40%.
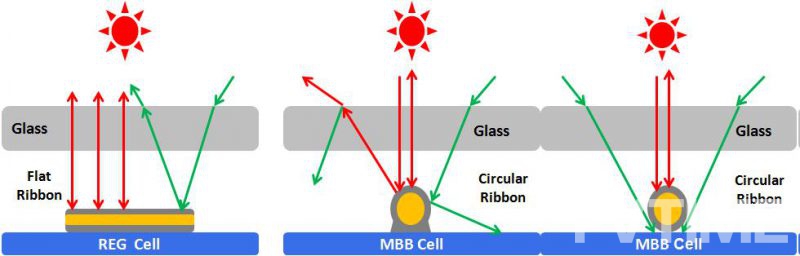
MBB module is also known for its high reliability. Closer busbar design reduces micro crack risk by decreasing residual stress. Even in the case of micro-cracks or deformation, the shorter distance between busbars decreases loss ratio of the cell and enables it to keep generating electricity. Additionally, the latticed design of busbars and fingers distributes inner stress evenly and reduces the risks of micro-cracks. When dealing with micro-cracks, the structure maintains high electricity-collecting capability and lowers thermal resistance risk caused by micro crack under normal working conditions. Mechanical load test (5400 Pa) shows that -micro-cracks could cause a degradation of 0.5% for conventional modules, while only 0.1% for MBB modules.
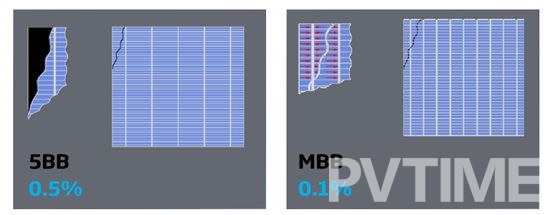
Integrating the advantages of high efficiency and reliability, the MBB technology can also control the cost by reducing the amount of silver paste.
Because of its advanced development and great efficiency improvement, half-cell technology has been adopted by most photovoltaic enterprises. The so-called half-cell technology is to cut the standard cell equally into two parts along the direction perpendicular to the busbar with the laser cutting method. Through this way, the current flowing through the busbar can be reduced to half the amount as a full-sized cell.
When the half-cut cells are connected in series, the resistance on the positive and negative circuits remain the same, so the power loss will be reduced to one-fourth of the previous level (Ploss=1/4*I2R), which ultimately reduces the power loss of the module, and improves its packaging efficiency and fill factor. Generally, half-cell module’s power can be 5-10W (1.6%-3.3%) or even higher than traditional module of the same size. Little difficulty and investment in retrofitting half-cell module production line and high yield make it a differentiated product and highly sought by producers.
Relevant experiments and projects also show that when the module is shaded, the special structure design of half-cell module can reduce the power loss of the module and perform better than regular modules.
The first-line producers’ average mass production power of 72-cell 9BB half-cell PERC modules with 158.75mm cells reaches 410W, and that of 78-cell module can reach 445W.
The combination of MBB and half-cell technology reduces the micro crack influence area by 50% compared with regular cells.
MBB and half-cell structure also lowers the module’s hotspot risk. Under the simulated condition of 1000W/m2 irradiation, 25 ℃ ambient temperature and 10W/m2·℃ convective heat transfer coefficient on the front and back of the module (with good ventilation), the heat dissipation effect of MBB half-cell module is better than that of the conventional module (which has relatively lower effective heat density), and the hotspot temperature is 27 ℃ lower than that of conventional module. In addition, the working temperature of MBB half-cell module is 2-3 ℃ lower than that of the regular module, and the power loss of working temperature is lower. It effectively reduces soiling loss caused by snow, dust and dirt, and energy loss caused by shielding, resulting in more stable power output.
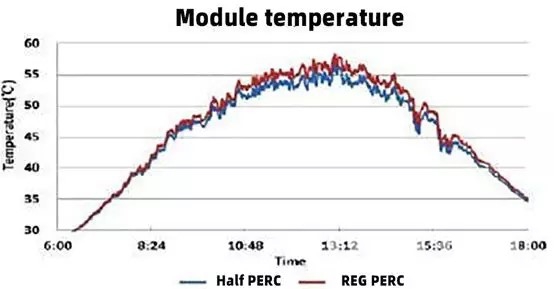
After the rigorous tests of loading, TC600 and dynamic loading with TC50 and HF10, the EL of half-cell MBB large-CELL module remains normal.
With its lower working temperature, better temperature coefficient and IAM, the half-cell MBB module with 158.75mm cells demonstrates its advantage of electricity-generating capability by increasing electricity by 1% during the testing period of one month. With a slight increase in cost, the module can bring higher benefits to users and achieve lower LCOE.
From the perspective of solar plant investors, the size of 158.75mm is the most cost-effective size in the entire industry at present. By combining with MBB and half-cell technology, the module assembled with 158.75 cells strengthens its value proposition, including (i) higher power and energy yield; (ii) greater reliability; and (iii) lower BOS cost and LCOE. The broad application of the module can help accelerate the launch of price bidding and grid parity projects, thus further promoting the development of the solar industry.