PVTIME – 158.75mm, 166mm, or 210mm, which is the better choice for the PV industry? The discussion started in 2019 and continues on.
Wafer sizes and technologies are broadly discussed, but once the wafers and cells are assembled into modules, the major concerns among the market participants are module and system performance, LCOE, investment return, and whether these modules could meet the high standards of price bidding and grid parity projects.
For solar power plant investors, pursuing larger sizes for the sake of price to module efficiency and transportation convenience isn’t a great idea. Instead, factors such as energy density and reliability are their primary concerns. As a result, modules with lower LCOE are more favorable among different emerging technologies.
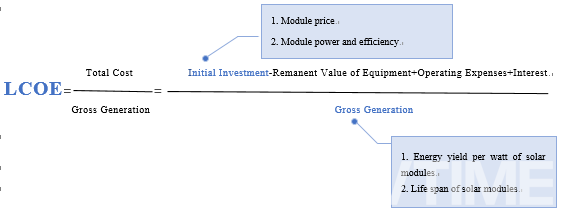
To achieve lower LCOE, reducing BOS costs and increasing energy yield are crucial. For the latter, the per-watt energy yield capability and lifespan/reliability of modules are the key factors and a solar module combining 158.75mm full square mono cells with MBB and half-cell technologies (158.75 MBB half-cell module) is considered as a perfect option for lowering LCOE. When compared with 166 and 210 modules, the 158.75 module is more compatible with current PV systems, thus reducing cost per watt with lower costs on installation and mounting brackets. This technology combination allows for the higher power output in modules, with 72-cell modules produced by leading suppliers reaching 410W, and 78-cell modules achieving 445W.
The energy yield capability of a 158.75 module is competitive and when compared with a 166 module, permits lower operating temperature, better system compatibility, higher DC/AC ratio, system efficiency, and more reliable performance.
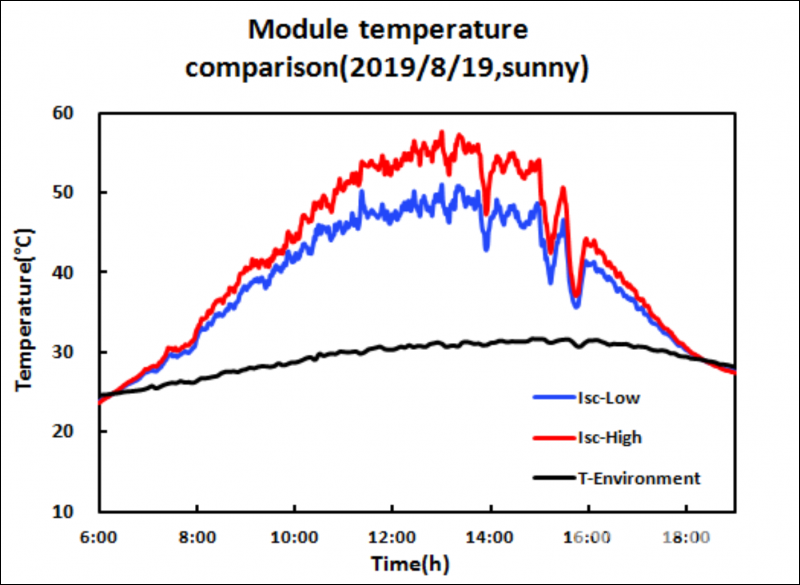
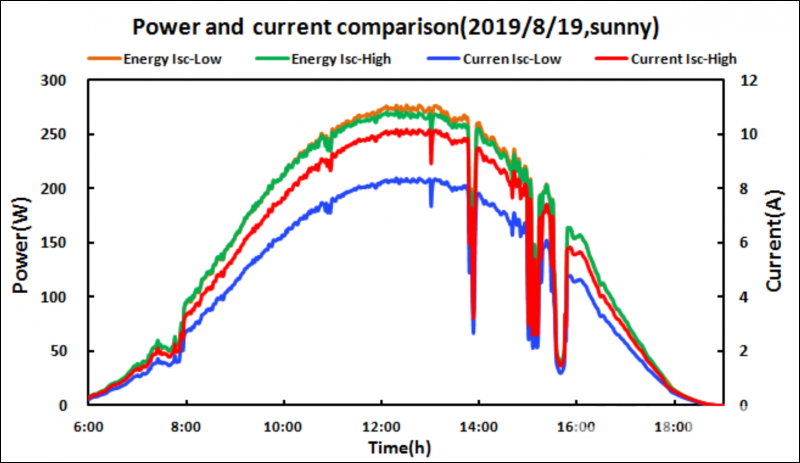
The above data indicates that the Current Isc-Low of 158.75 modules is 5℃ lower than the Current Isc-High of 166 modules in terms of operating temperature, and the output efficiency of the former is 2% higher. The high-current, high operating temperature, and high risks of hot spots of 166 modules negatively impacts its lifespan and performance.
The lifespan of a solar module’s encapsulation material closely correlates with its operating temperature. According to Arrhenius Equation, when the operating temperature is increased by 10℃, the aging rate is doubled and the service life is reduced by half. As the operating temperature of 158.75 module is 5℃ lower, it’s more reliable and will have a longer lifespan.
It is known that string inverters would raise the operating voltage to decrease the output of working current when the input current overruns the upper limit of 13A. Therefore, bifacial module with M6 cells would face the problem of yield limitation during the peak hours of irradiation, which is known as peak clipping. As 158.75 module perfectly matches the mainstream string inverters, there is no peak clipping for 158.75 modules.
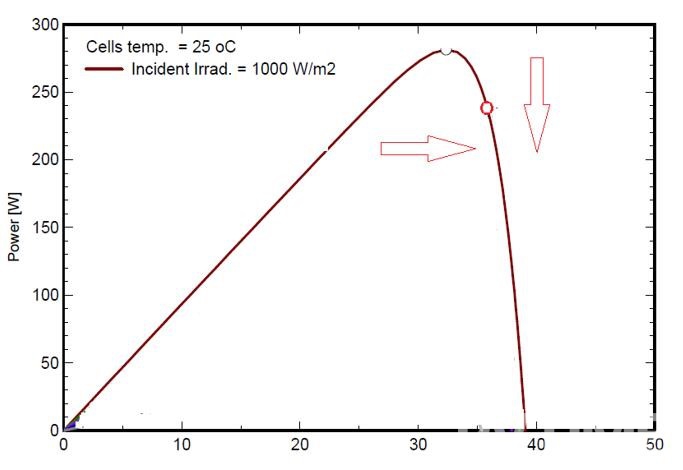
A high DC/AC ratio system within the safety margin is another crucial factor for decreasing LCOE and would help reduce BOS cost (system costs related to DC/AC ratio, including inverters, box transformer substation, other boosting equipment, and cables, etc.), which accounts for around 33% of the total of system costs. An increase of 5% in the DC/AC ratio would lead to a decrease of 0.035-0.05yuan/Wp in system costs. Moreover, 158.75 module allows more flexibility than 166 while operating with a centralized inverter. In the design scheme of a project in China shown below, we can see that the DC/AC ratio of 78-cell 158.75 MBB half-cell modules is much higher than that of M6 modules..
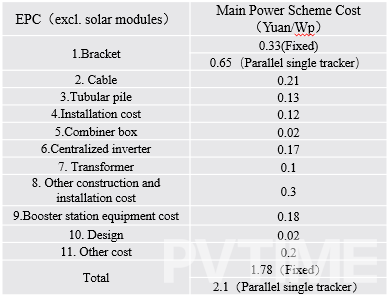
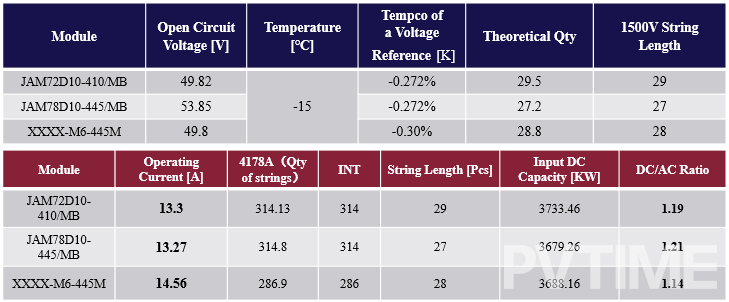
According to PVSYST simulation experiment on a parallel single tracker system, taking the adjusted voltage values under low irradiance into consideration, the 158.75 module outperforms the M6 module and has longer generating hours. In terms of system efficiency, the 166 module is about 0.7% lower than that of the 158.75 module.
Besides, the 158.75 module is more compatible with the bearing capacity of current brackets, and is easier to transport and install.
In general, the excellent performance of 158.75mm on the system side makes the 158.75 products favored by module suppliers and is highly recognized by the market.
The year 2020 is crucial for the photovoltaic industry to rid its reliance on subsidies. The industry can accelerate the pace of reaching grid parity by continuously reducing system costs, increasing system power generation, and decreasing LCOE. Furthermore, the industry should not place emphasis on the size of wafers unilaterally, but take into consideration the downstream factors such as system compatibility and lower LCOE in order to promote the development of the industry rationally.